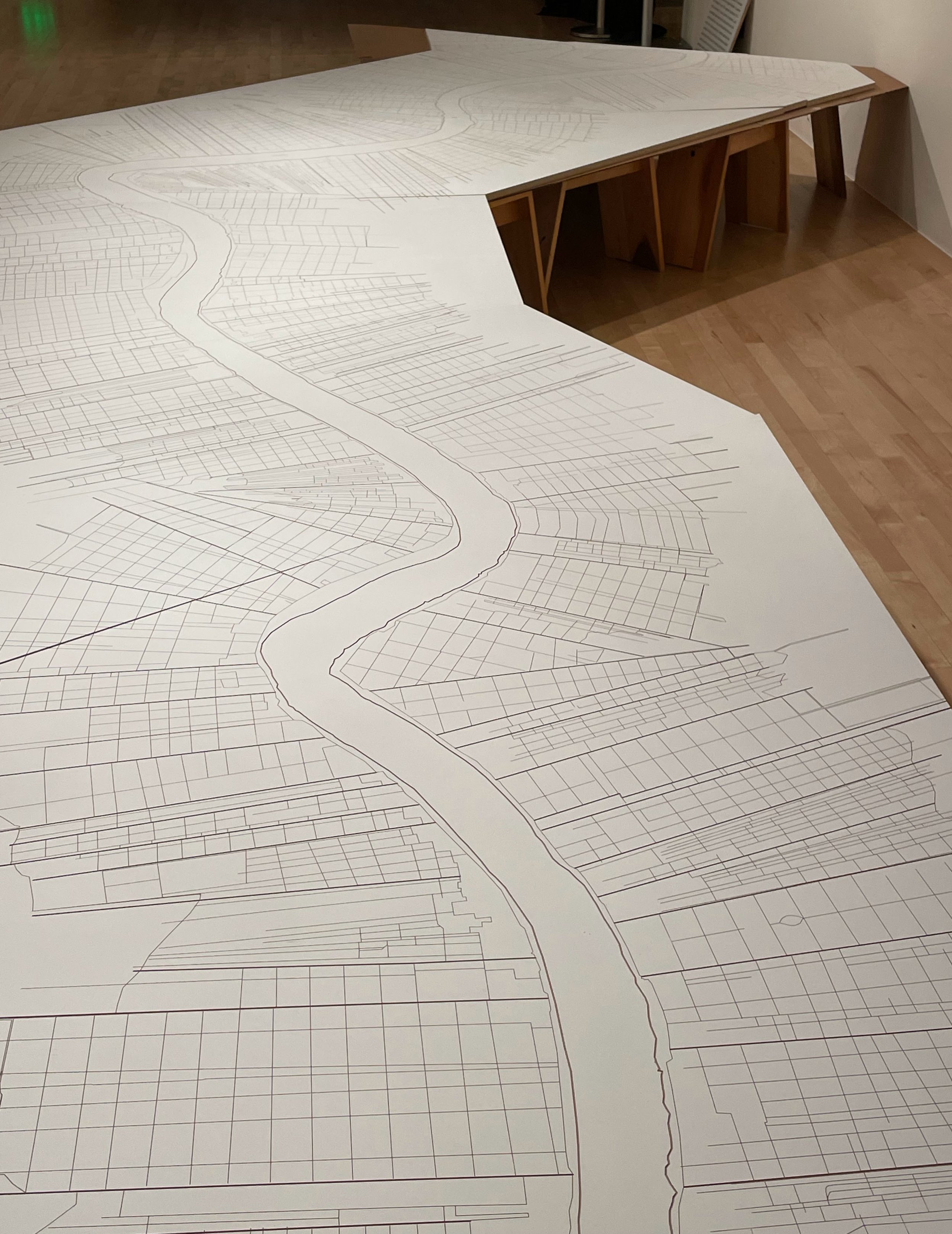
Strategic Vendor Management & Technical Integration
3D Map Installation
Leading Complex Multi-Phase Projects Through Strategic Pivots
The Challenge
Situation: Lead a complex 5-month fabrication and technical integration project requiring coordination between multiple external vendors, internal teams, and cross-institutional stakeholders while maintaining artistic vision and technical specifications.
Project Scope:
23' x 9' large-scale physical installation
Multi-phase project: external fabrication + internal technical integration
Complex stakeholder management across institutions
Budget optimization requirements mid-project
Technical specifications requiring specialized fabrication expertise
Key Constraints:
Original fabrication approach proving cost-prohibitive
Technical specifications requiring precision manufacturing
Timeline pressures with multiple dependencies
Cross-institutional approval processes
Integration of physical and digital components
Strategic Planning & Vendor Management
Vendor Evaluation & Selection:
Conducted comprehensive vendor analysis for specialized CNC fabrication capabilities
Evaluated technical capabilities against artistic requirements
Managed vendor relationships through daily communication protocols
Created vendor performance monitoring and quality assurance frameworks
Requirements Analysis:
Translated artistic vision into technical specifications
Identified critical path dependencies between fabrication and integration phases
Established quality standards for large-scale precision manufacturing
Created detailed project timeline with milestone tracking
Process Optimization & Strategic Pivots
Mid-Project Strategic Redesign:
Challenge: Original laser cutting approach proved cost-prohibitive and technically limiting
Analysis: Evaluated alternative manufacturing methods and material options
Solution: Pivoted to CNC fabrication with strategic material substitution
Process: Managed stakeholder communication and approval for significant approach change
Cost Optimization:
Shifted from expensive architectural panels to painted MDF substrate
Negotiated with new fabrication vendor for optimized pricing
Result: Achieved 50% cost reduction while maintaining artistic integrity
Created reusable cost-benefit analysis framework for future projects
Quality Assurance:
Established design iteration protocols for continuous refinement
Created file modification and version control systems
Implemented real-time problem-solving processes
Maintained quality standards through manufacturing approach changes
Cross-Functional Team Leadership
Stakeholder Management:
Managed daily communication with multiple external fabricators
Coordinated cross-institutional stakeholder approvals
Balanced artistic vision with technical and budget constraints
Created transparent communication channels for complex decision-making
Multi-Phase Project Coordination:
Phase 1: External fabrication management and quality control
Phase 2: Internal technical integration and multimedia implementation
Seamless handoff protocols between external and internal teams
Resource allocation optimization across project phases
Technical Integration Leadership:
Led internal team through complex construction and technical implementation
Coordinated integration of CNC-fabricated elements with projection systems
Managed precise technical specifications for multimedia components
Created documentation for complex technical assembly processes
Technical Innovation & Problem Solving
Manufacturing Process Innovation:
Developed hybrid approach combining external specialized fabrication with internal technical integration
Created workflow optimization for large-scale physical-digital integration
Established quality control protocols for precision manufacturing
Built knowledge management systems for complex technical processes
Technical Integration:
Designed integration system for 3 vertical projectors with physical installation
Created precise coordination protocols for construction and technical elements
Developed testing and calibration procedures for multimedia components
Established maintenance and troubleshooting documentation
Results & Organizational Impact
Project Delivery:
Successful completion of complex 5-month multi-phase project
50% cost reduction through strategic process redesign
Maintained artistic integrity while achieving technical optimization
On-time delivery despite significant mid-project strategic changes
Process Innovation:
Created reusable vendor evaluation framework for complex fabrication projects
Developed cost-benefit analysis methodology for strategic decision-making
Established quality assurance protocols for large-scale manufacturing
Built stakeholder communication framework for complex multi-institutional projects
Team Development:
Enhanced cross-functional collaboration between creative and technical teams
Improved vendor relationship management capabilities
Developed agile project management competencies for complex pivots
Created knowledge documentation for technical integration processes
Organizational Capabilities:
Demonstrated strategic flexibility in response to project constraints
Improved cost optimization processes for future projects
Enhanced technical integration capabilities
Strengthened vendor management and relationship building
Key Skills Demonstrated
Strategic Decision-Making: Successfully pivoted manufacturing approach mid-project Vendor Management:Coordinated multiple external fabricators with daily communication Cost Optimization: Achieved 50% cost reduction through strategic redesign Cross-Functional Leadership: Managed both external fabrication and internal technical teamsTechnical Integration: Led complex physical-digital system integration Stakeholder Management: Balanced artistic vision with technical and budget constraints Quality Assurance: Maintained standards through significant process changes Project Coordination: Successfully managed complex multi-phase project timeline